Buy Jindal Hissar Steel Pipes at Indosup
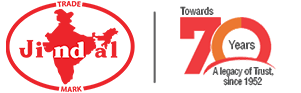
Indosup is the largest procurement partner for Jindal Hissar steel pipes.
Jindal Hissar Steel Pipes have become a trusted name in the steel pipe industry. Known for their high-quality products, Jindal Hissar offers a variety of steel pipes designed to meet the needs of diverse industries such as construction, plumbing, gas distribution, and industrial infrastructure
Email your inquiries to sales@indosup.com
OR
Whatsapp your inquiries to +91 9599610007
Why Choose Indosup for the Procurement of Jindal Hissar steel Pipes?
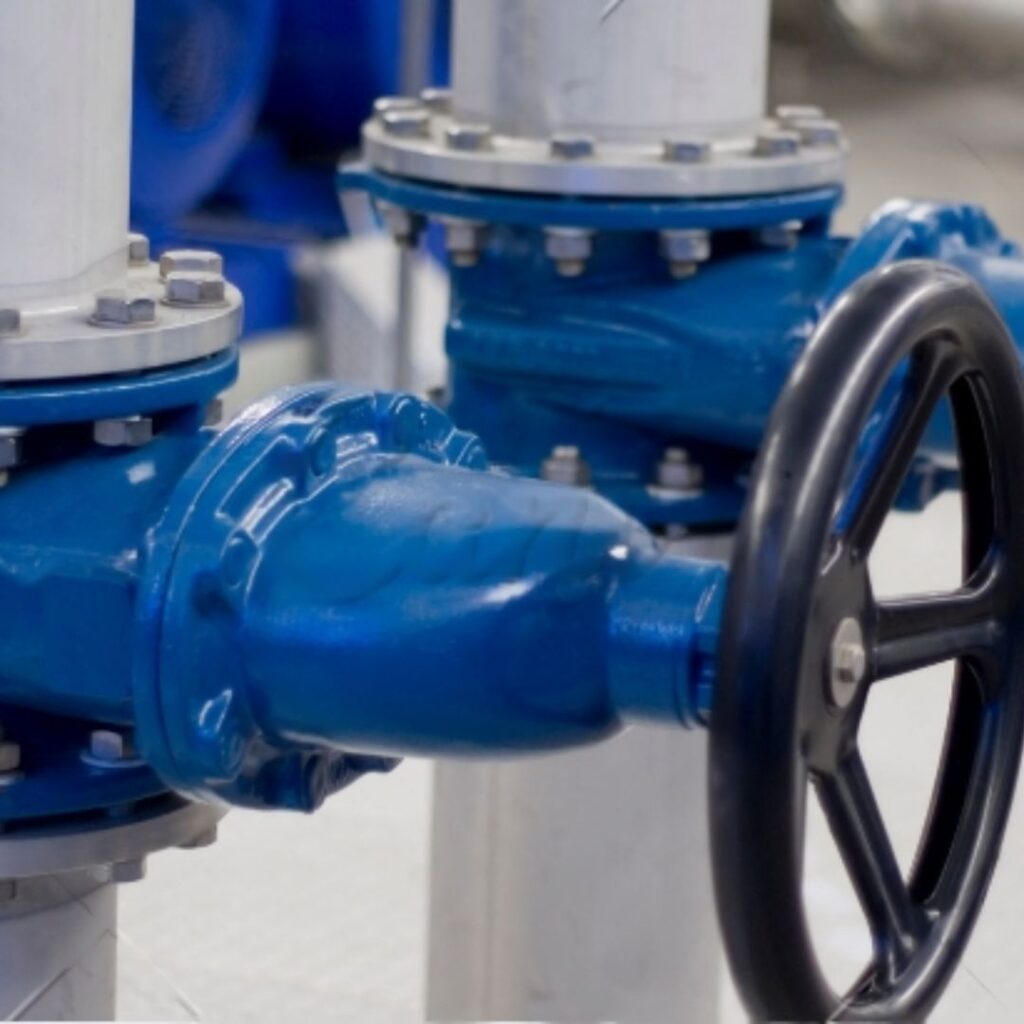
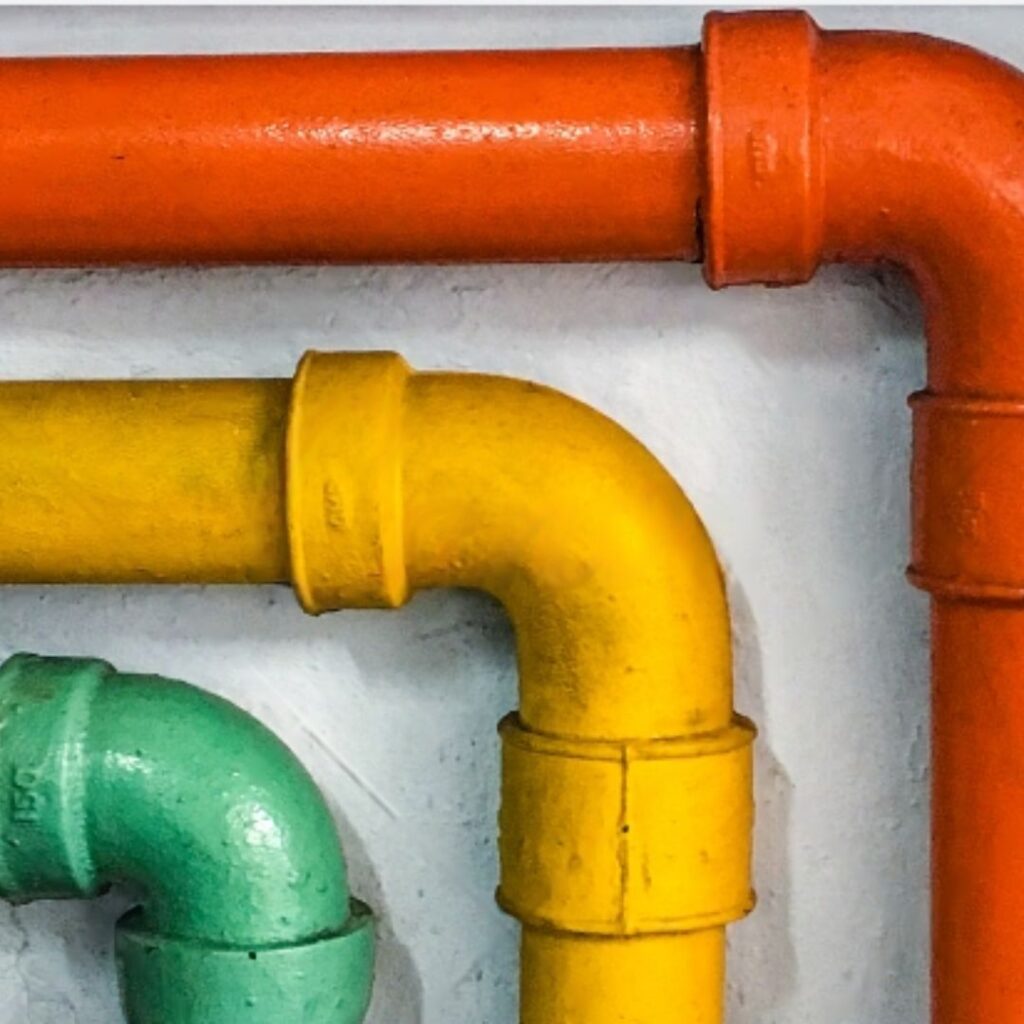
Jindal Hissar Steel Pipes are manufactured by Jindal Stainless (Hisar) Limited, part of the renowned Jindal Group, one of India’s largest producers of stainless steel.
These pipes are known for their durability, strength, and versatility, making them suitable for a wide range of uses in both residential and industrial settings.
Types of Jindal Hissar Steel Pipes
1. Stainless Steel Pipes
Jindal Hissar’s stainless steel pipes are renowned for their high resistance to corrosion and extreme temperatures.
They are widely used in industries such as chemical processing, oil and gas, water treatment, and food processing, where hygiene and resistance to chemical corrosion are crucial.
- Applications of Stainless Steel Pipes:
- Food and beverage processing industries
- Chemical and petrochemical plants
- Water treatment facilities
- Medical and pharmaceutical industries
- Construction of structures exposed to harsh weather
2. Mild Steel (MS) Pipes
Mild steel pipes are known for their flexibility, ductility, and affordability, making them suitable for a wide range of applications.
Jindal Hissar’s MS pipes are extensively used in structural applications, fabrication, and general engineering purposes. These pipes can be easily welded and shaped to meet the requirements of various projects.
- Applications of MS Pipes:
- Construction and infrastructure development
- Industrial pipelines for water, gas, and steam
- Fencing and boundary applications
- Automobile and mechanical components
- General fabrication and metalwork
3. Galvanized Iron (GI) Pipes
Galvanized Iron pipes are mild steel pipes coated with a layer of zinc to prevent rusting and corrosion.
Jindal Hissar’s GI pipes are widely used for water supply, gas distribution, and drainage systems. The zinc coating provides excellent protection against rust, making GI pipes a durable and cost-effective solution for outdoor and underground applications.
- Applications of GI Pipes:
- Plumbing and water supply systems
- Fire-fighting networks
- Gas distribution lines
- Drainage systems
- Irrigation and agricultural applications
4.Jindal Hissar Steel Pipes: Hollow Sections
These structural steel profiles are known for their strength, stability, and versatility, making them ideal for construction, furniture manufacturing, automotive components, and agricultural equipment.
Hollow sections provide a lightweight solution with excellent load-bearing capabilities and aesthetic appeal. Their cost-effectiveness and diverse applications make Jindal Hissar hollow sections a preferred choice for engineers and architects in various industries.
5.APL 5L Grade B Pipes
APL 5L Grade B pipes are a specific type of steel pipe designed for transporting fluids in high-pressure applications.
Manufactured according to the American Petroleum Institute (API) specifications, these pipes are widely used in the oil and gas industry.
Below is an overview of APL 5L Grade B pipes offered by Jindal Hissar.
Applications
- Oil and Gas Transportation
- Water Supply Systems
- Refinery and Petrochemical Industries
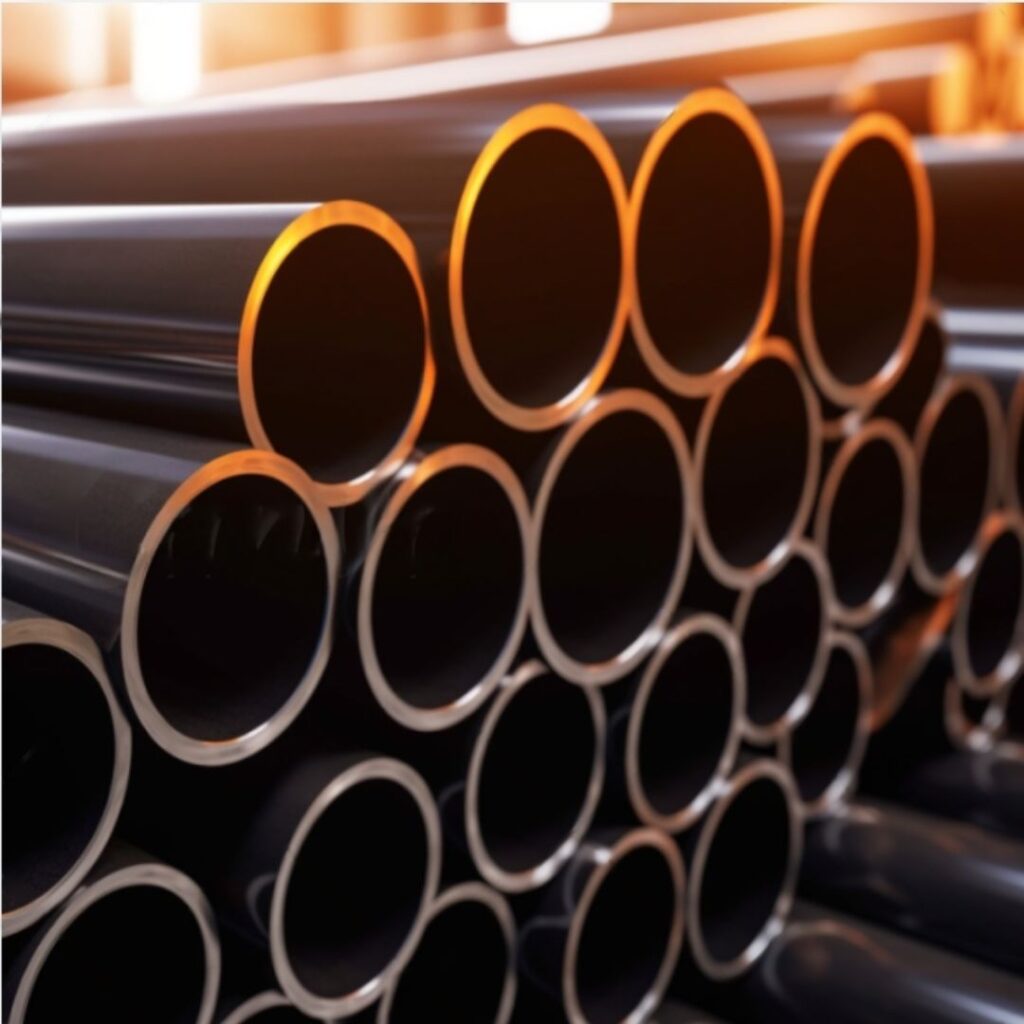
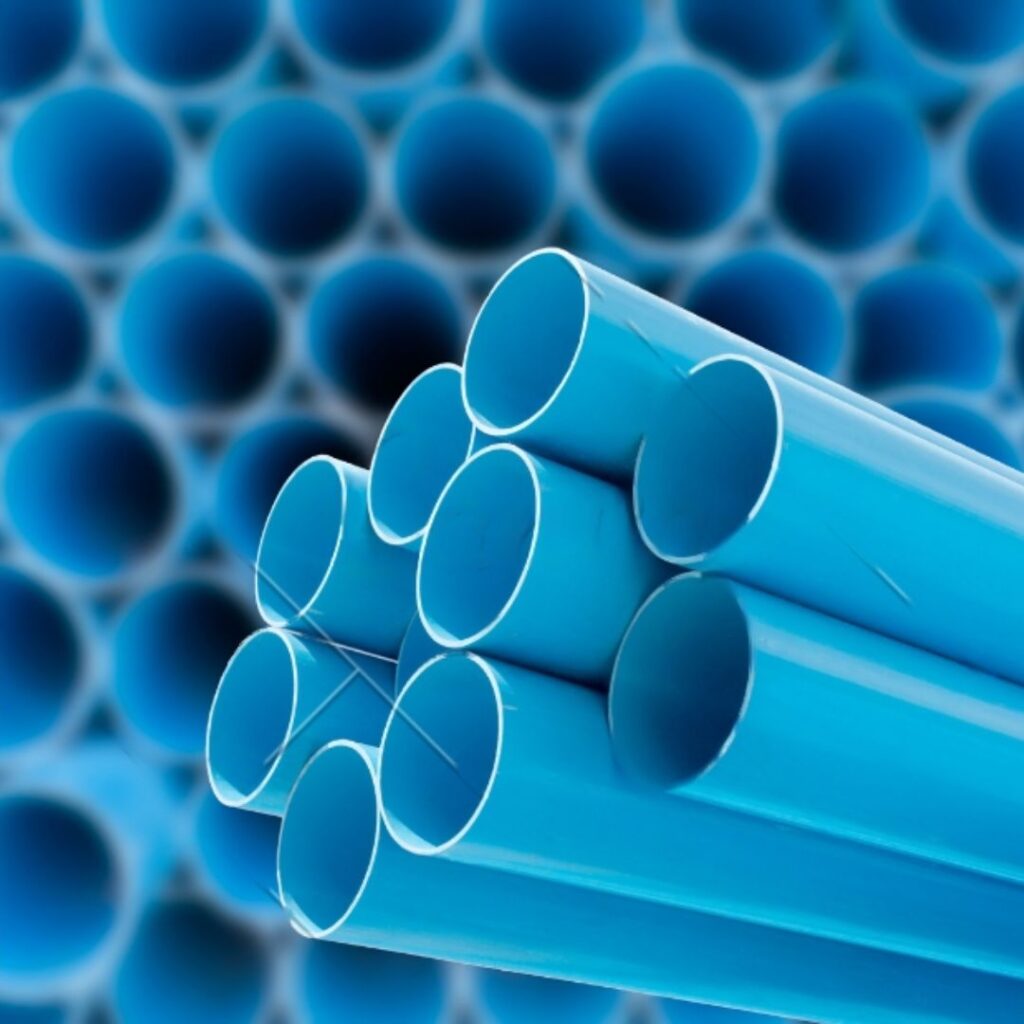
Jindal Hissar Steel Pipes: Indian and International Standards
Jindal Hissar Steel Pipes adhere to both Indian and international standards to ensure the highest levels of quality, safety, and performance. These standards define the specifications for various grades, dimensions, and testing procedures of steel pipes.
1. Indian Standards (IS)
IS 1239 (Part 1): Specification for mild steel tubes, tubulars, and other wrought steel fittings.
- Application: Used for water, gas, air, and steam services.
IS 3589: Specification for steel pipes for water and sewage.
- Application: Used for water supply systems and sewage lines.
IS 1161: Specification for steel tubes for structural purposes.
- Application: Used in the construction of buildings, bridges, and other structures.
IS 4923: Specification for hollow steel sections for structural use.
- Application: Hollow sections for construction, engineering, and fabrication purposes.
IS 1978: Specification for high tensile steel pipes.
- Application: Used for high-pressure services, including transportation of gases and liquids.
2. International Standards
API 5L: Specification for line pipes used in the transportation of oil, gas, and water in the petroleum and natural gas industries.
- Application: APL 5L pipes are used in pipeline systems across the world for fluid transportation.
ASTM A53: Standard specification for pipe, steel, black and hot-dipped, zinc-coated, welded, and seamless.
- Application: General piping applications for fluids and gases, particularly in mechanical and pressure applications.
ASTM A106: Standard specification for seamless carbon steel pipe for high-temperature service.
- Application: Used for boilers, pressure vessels, and piping systems that handle high temperatures.
ASTM A500: Standard specification for cold-formed welded and seamless carbon steel structural tubing.
- Application: Used for structural applications like building construction, bridges, and engineering projects.
EN 10219: European standard for cold-formed welded structural hollow sections of non-alloy and fine grain steels.
- Application: Used for construction and engineering applications where strength is critical.
DIN 2440: German standard for steel tubes suitable for welding and threading.
- Application: Used for general engineering purposes and in the construction of pipelines.
Understanding the Manufacturing Process of Jindal Hissar Steel Pipes
Jindal Hissar, a major player in India’s steel industry, produces a range of steel pipes, primarily focusing on seamless and welded pipes. The manufacturing process for these steel pipes generally follows industry-standard steps, including both material preparation and production stages, which can be summarized as follows:
1. Raw Material Selection
The process starts with selecting high-quality raw materials, typically billets for seamless pipes and hot-rolled coils or strips for welded pipes. The type of steel used is often low carbon or alloy steel, depending on the application.
2. Heating and Piercing (For Seamless Pipes)
- Billet Heating: For seamless pipes, steel billets are heated in a furnace until they reach the right temperature for deformation (above 1200°C).
- Piercing: The hot billet is then fed into a piercing mill where it’s pierced at the center by a rotating mandrel or piercer, creating a hollow tube. This is the first stage of shaping the pipe.
3. Forming the Pipe (For Welded Pipes)
- Strip Preparation: For welded pipes, steel strips are shaped into tubular forms by passing them through a series of rollers that gradually curve the strip into a cylindrical shape.
- Welding: Once the strip is formed into a tube, the edges are welded together using either an electric resistance welding (ERW) or submerged arc welding (SAW) process, depending on the pipe type and size.
- ERW: Primarily used for smaller diameter pipes, where the edges of the steel strip are fused through heat generated by electrical resistance.
- SAW: More common for larger diameter pipes, where an arc is submerged under a layer of flux, protecting the weld from contamination.
4. Elongation (For Seamless Pipes)
- After piercing, the hollow tube is elongated by passing it through rolling mills to achieve the required length and diameter. This process is known as the elongation stage and involves continuous rotation and rolling, reducing the wall thickness and expanding the diameter of the tube.
5. Heat Treatment
Both seamless and welded pipes may undergo heat treatment processes like normalizing, quenching, and tempering to achieve the desired mechanical properties, such as strength, toughness, and hardness. The heat treatment also improves the pipe’s resistance to corrosion and stress.
6. Sizing and Shaping
- The pipes are then passed through sizing mills to ensure the correct diameter and wall thickness. In this process, the outer diameter is fine-tuned to meet precise specifications.
- For welded pipes, non-destructive testing is carried out to ensure the weld quality is flawless.
7. Cutting
The long steel pipes are cut into specific lengths using automated cutting machines. This ensures uniform pipe sizes based on customer requirements.
8. Surface Treatment
- The pipes often go through surface treatments such as pickling, galvanizing, or coating to prevent rust and corrosion.
- Galvanization (applying a protective zinc coating) is common for pipes used in corrosive environments like plumbing, oil & gas, and water supply systems.
9. Testing and Inspection
Stringent quality control tests are conducted to ensure that the pipes meet industry standards. These tests include:
- Ultrasonic Testing: To check for internal defects.
- Hydrostatic Testing: To ensure the pipe can withstand high pressures.
- X-ray Inspection: For welded pipes, to check the weld quality.
- Dimensional Checks: To verify the diameter, wall thickness, and overall size of the pipes.
10. Finishing and Packaging
The pipes are marked with identification tags, painted or coated (if required), and packed securely for shipment. They are bundled or palletized depending on their size and customer needs.
11. Logistics and Shipping
After production and quality control checks, the pipes are loaded and shipped to various sectors, including oil & gas, construction, infrastructure, and other industrial applications.
Jindal Hissar maintains a strict quality control system throughout this process to ensure their pipes meet global standards, such as ASTM, DIN, API, and IS, among others.
Email your inquiries to sales@indosup.com
OR
Whatsapp your inquiries to +91 9599610007